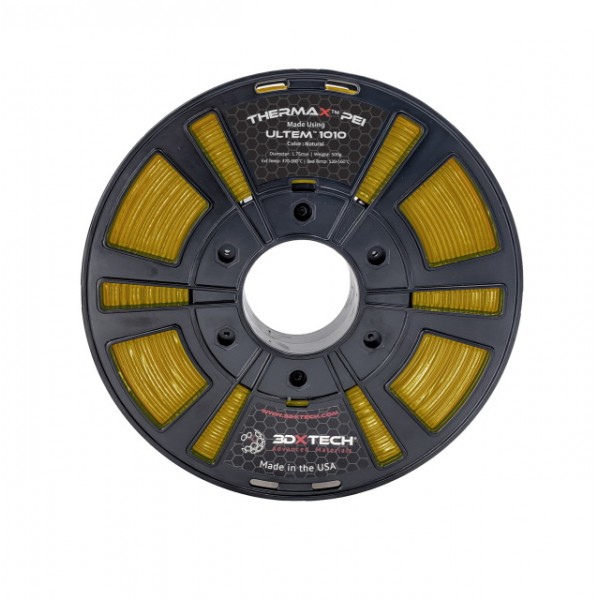
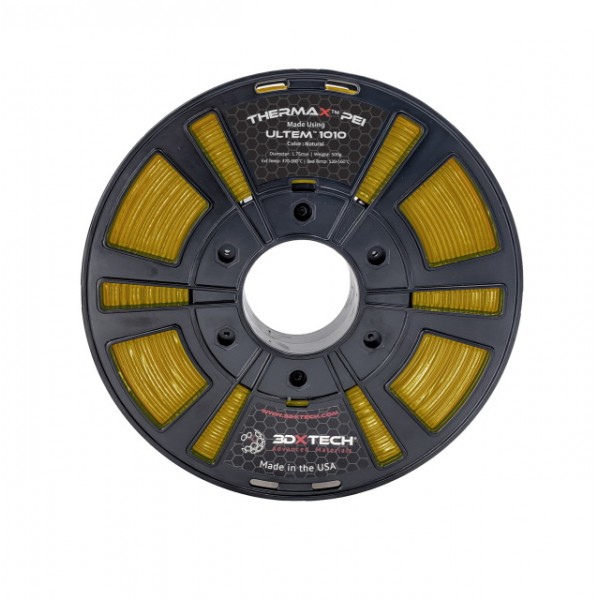
3DXTech FibreX™ Ultem 1010 is a high-quality (PEI) filament with excellent thermal and chemical resistance properties, as well as great dimensional stability. An ideal choice for a range of demanding applications.
Kostenloser lebenslanger Remote-Support für alle Produkte
Fragen Sie uns nach unseren Bildungsrabatten
3DXTech manufacture this ultra-performance 3D printing filament using ULTEM 1010 PEI (polyether imide) resin. PEI is an amorphous, high-performance polymer that combines excellent thermal properties, exceptional dimensional stability, inherent flame retardancy, and good chemical resistance. Filaments made using ULTEM 1010 resin offer the ability to create parts with excellent properties at elevated temperatures due to a high glass transition temperature (Tg) of 217°C.
Nozzle Temperature | Build Plate Temperature | Heated Build Chamber | Bed Adhesion |
---|---|---|---|
370-390°C | 120-160°C | Recommended | PEI tape or gluestick applied to glass |
Due to the nature of 3D printing with Ultem, residual stresses may be present in the printed part which can affect the mechanical properties. These residual stresses can be reduced by using a hot-air oven to anneal the parts. Please see the steps below as a guide for annealing 3D printed Ultem/PEI parts: